Qu’est-ce que le DRP (distribution requirement planning) ?
En logistique, de nombreux facteurs concourent à la réussite d’un plan d’exigences de distribution et de la chaîne d’approvisionnement. En termes de réductions de coûts en entreprise, l’utilisation d’un système DRP (Distribution Requirement Planning) peut constituer l‘alternative adaptée pour répondre efficacement à la demande des clients. Que faut-il savoir sur le DRP en supply chain ? Comment un système DRP peut-il contribuer à la gestion des stocks dans une entreprise ? Voici quelques éléments de réponses face à vos différentes préoccupations.
Distribution Requirement Planning (DRP) : qu’est-ce que c’est ?
Littéralement, le sigle DRP signifie la « planification des ressources de distribution ». Le DRP est un système qui a pour but d’optimiser efficacement le service de livraison et les stocks dans un processus de distribution de marchandises. La planification des besoins de distribution de marchandises ou le DRP peut se définir comme une méthode de calcul des quantités des produits manufacturés à expédier au niveau de chaque centre logistique ou entrepôt.
Il s’agit d’un système efficace pour avoir une idée précise des ressources financières et logistiques afin de mieux satisfaire la demande des clients. La planification des ressources de distribution permet également aux entreprises d’éviter les ruptures de stock. Ce système s’appuie sur l’ensemble des stocks déclarés en fichiers dans les lieux de stockage et dans les différents dépôts de l’entreprise.
Le DRP s’appuie également sur les prévisions de consommations. Cela permet notamment aux entreprises qui ont une activité de distribution d’optimiser efficacement leurs flux depuis la demande.
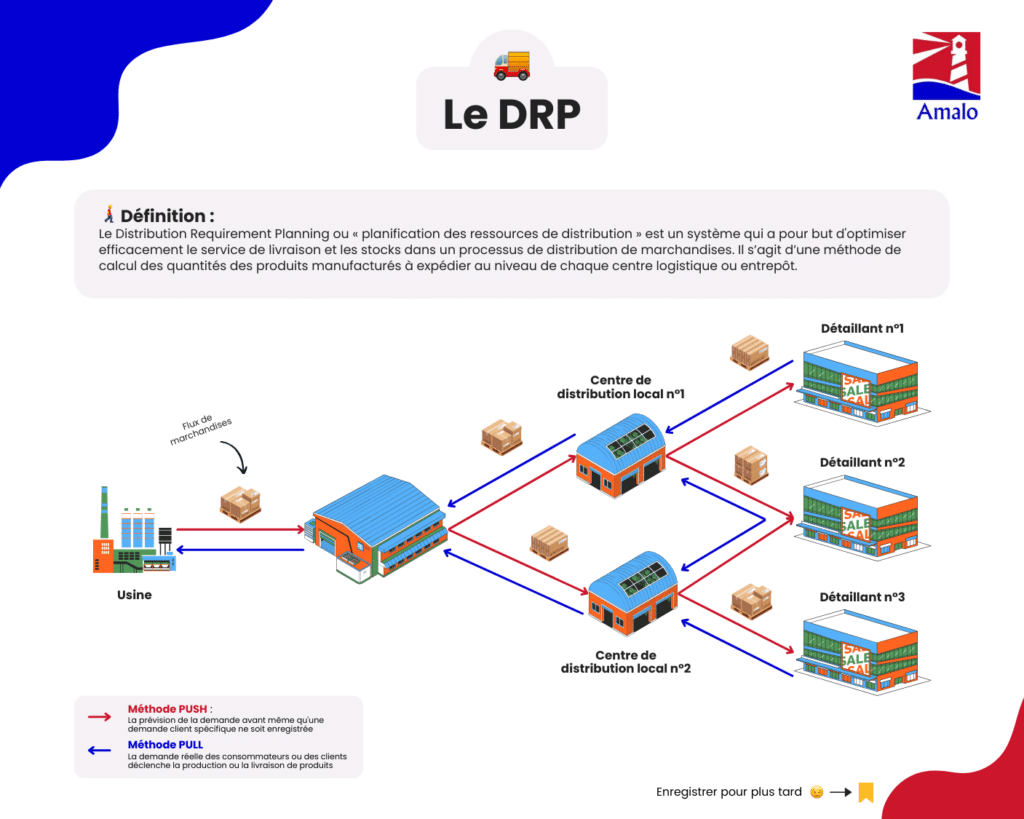
Quels sont les avantages d’un système DRP pour la supply chain ?
L’utilisation d’un système DRP recèle de nombreux avantages pour les entreprises ayant une activité de distribution (magasins de vente, dépôts, centres de distribution…). En effet, la planification des ressources de distribution permet d’améliorer le service client. Il tire ses informations du marché en vue de permettre à ces entreprises de distribution de garantir des sources d’approvisionnement en marchandises répondant à la demande. Cela agit sur la satisfaction et la fidélité des clients.
Avec un tel système, les entreprises de distribution peuvent avoir des informations relatives :
- au service après-vente,
- aux demandes des clients,
- à l’évolution des produits,
- aux tendances du marché.
Cela permettra d’entreprendre des actions de planification en approvisionnement et en production pour synchroniser la demande et l’offre. Dans le cas où un article devient populaire de façon soudaine, l’entreprise peut augmenter la production du produit grâce au système DRP. Par contre, si l’article devient soudainement moins populaire, la planification des besoins de distribution peut aider les entreprises à réduire la production.
L’utilisation d’un système DRP représente ainsi une solution efficace pour minimiser les pénuries et distribuer les produits efficacement et le plus rapidement possible. En matière de gestion de stock, le DRP favorise la maîtrise des coûts en rapport avec la production, le transport et le service de livraison. L’utilisation d’un système DRP permet d’optimiser tous les niveaux de stock et peut notamment aider les entreprises à prendre des décisions rapidement en fonction des tendances du marché.
Comment le DRP peut-il aider à la gestion des stocks ?
Un système DRP présente approximativement les mêmes fonctionnalités que la planification des besoins en matériel (MRP). Le MRP et le DRP se basent tous deux sur une prévision des demandes afin de se conformer aux besoins du marché. La planification des ressources de distribution utilise une structure arborescente où un entrepôt se charge de l’approvisionnement des installations régionales. À leur tour, ces installations en approvisionnent d’autres et la structure peut posséder n’importe quel nombre de couches. La distribution DRP fonctionne selon deux techniques distinctes : la méthode pull et la méthode push.
Découvrez le métier de 👉 prévisionniste des ventes
La méthode pull
La distribution DRP selon la méthode pull (flux tiré) adapte la production de chaque article à la demande réelle. Ce processus de production à la demande fait remonter les marchandises ou les articles à travers le réseau tout en prenant en charge les commandes des clients. La disponibilité des marchandises est donc contrôlée par la gestion locale. Ce qui offre notamment une meilleure disponibilité aux clients.
La méthode pull permet aux entreprises de réduire les coûts de stockage et d’éviter la surproduction. En supply chain, cette méthode permet d’optimiser les coûts de logistique tout en supprimant les processus qui peuvent se révéler inutiles. Avec cette technique, il est possible de personnaliser un article ou un produit en fonction des besoins du client. Il s’agit d’un choix adapté aux entreprises désireuses d’opter pour des solutions logistiques durables. Cela leur permet de réduire leur impact écologique en ce qui concerne le mode de fabrication des produits ou leur stockage.
Il peut être cependant difficile de gérer le stock de distribution dans un système pull. La demande remonte le réseau et chaque commande est nouvelle pour le centre d’approvisionnement. Quant au temps de production des marchandises, il est généralement plus long et il faudra avertir les clients en conséquence.
La méthode push
Contrairement à la méthode pull, la technique de distribution push (flux poussé) est basée sur la prévision de la demande. Les produits et les articles sont fabriqués à l’avance. La méthode push favorise la maîtrise des coûts logistiques dans la mesure où il est possible de planifier les expéditions et les niveaux de stock. Les articles sont fabriqués en grande quantité, ce qui diminue les coûts de production par unité de produit.
Afin de s’adapter aux éventuelles variations de la demande, le système de production doit être flexible et rapide. Dans ce contexte, l’entreprise ayant des activités de distribution optimise son approvisionnement logistique, répond aux besoins des clients et réduit les coûts opérationnels.
L’inconvénient principal de la méthode push est lié aux risques en rapport avec d’éventuelles erreurs en matière de planification de la demande. La production peut largement dépasser la demande estimée (surstock) ou la demande peut dépasser les prévisions de vente (rupture de stock).
Dans le choix de la méthode de distribution, il faudra prendre en compte certains paramètres :
- la gestion des stocks,
- la capacité de stockage de l’entrepôt,
- le suivi du flux,
- la fiabilité du service,
- l’exécution des commandes.
La stratégie de production DRP adoptée doit rendre la chaîne d’approvisionnement plus efficace.
Comment assurer le management d’un système DRP ?
L’utilisation d’un système DRP peut permettre aux entreprises ayant des activités de distribution de répondre efficacement aux besoins des clients. Cette solution permet d’avoir des ressources suffisantes pour le centre de distribution et favorise une meilleure disponibilité des produits avec des coûts logistiques maîtrisés. Pour des résultats probants, il est important de bien planifier son réseau lorsqu’on opte pour le DRP. Les articles doivent être livrés dans les délais.
Concernant les exigences du marché, il est primordial d’avoir des données précises pour la création du plan de distribution. Pour l’acheminement des articles aux clients, un réseau de centres de distribution se révèle nécessaire. Il est également important d’assurer une bonne gestion des stocks. Cela permettra ainsi de réduire les pénuries et d’assurer que les produits soient disponibles pour les clients en cas de besoin. Le processus de prévision doit être surveillé de façon efficace.
La satisfaction des clients doit être maximisée et il faudra ajuster convenablement les emplacements des entrepôts. Le nombre d’emplacements pour le stockage des articles dépendra donc de la clientèle. Dans la gestion des stocks, les exigences de décaissement doivent être prises en compte et il est conseillé de définir des niveaux de stock de sécurité. Les exigences de distribution (délai de livraison, nombre de produits, dimensions et poids…) doivent être également prises en compte.
Vous recrutez ? Faites appel à un cabinet de recrutement en supply chain
Vous cherchez du travail ? Consultez nos offres d’emploi en supply chain